THE UNIMOG IMPLEMENT CARRIER.
A vehicle class of its own.
Many interfaces, year-round use, economical operation, safe on and off the road. The Unimog implement carrier - developed as a versatile top performer with one goal: to be as efficient as possible.
Its robustness and reliability, as well as its outstanding flexibility, have made the Unimog the implement carrier of choice for professionals for several decades now. The reason for that is that the "Universal-Motor-Gerät (universally applicable motorised device) - as it was originally known - is a vehicle which was specifically developed with these aims in mind. In conjunction with numerous implement and body manufacturers, as well as the great know-how of the Unimog partners, a system came into existence whose flexibility and productivity are unparalleled. Despite its broad scope of practical capabilities, its dimensions were able to be kept extremely compact - and it's for this specific reason that the Unimog can make use of its effectiveness virtually anywhere you need it - on and off the road.
THE UNIMOG U 219 - U 535 AT A GLACE.

Comfort.
A modern and practical cab helps to create a more comfortable working environment for drivers and operators. Find out more.

Drive Concept
More information about suspension, transmission, hydraulics and implement carrying capabilities.

Areas of application.
Unimog is unparalleled when it comes to versatility. Discover how the Unimog can be tailored for your business.

Technical data.
In this area, we will provide you with information on the technical details of all model variants of the Unimog implement carrier.

Highlights and other facts.
EasyDrive combines the advantages of a fuel-saving manual transmission for driving at speeds up to 89 km/h with a hydrostatic traction drive for working at speeds between 0.1 and 50 km/h.
Features
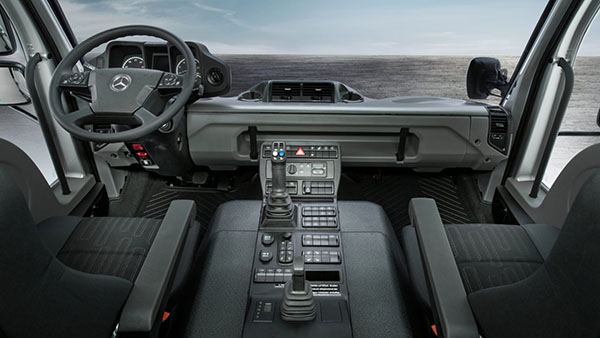
Makes living with Unimog a pleasure: the cab.
The Unimog is built to achieve great things. Unimog features a well-thought out and productive workplace for both driver and up to two crew members. The spacious cab and the flat cab floor provide ample head and leg room. The intuitive operating controls make daily operation more efficient. Controls are arranged so that they can be reached easily. A modular switch panel is installed in the centre console and its position can be altered as required.
Climb in. Feel good. Get going.
The Unimog implement carrier is one of the most modern workplaces around. It includes the standard height and tilt-adjustable steering column which allows for an optimal seating position. In conjunction with the low-vibration cab, the optional air-sprung driver's seat helps reduce fatigue. And anyone spending longer periods of time in the new cab comes to appreciate the powerful air-conditioning and heating system: regardless of the weather, it ensures comfortable temperatures inside the vehicle. What's more, in winter, the seat heating can be switched on.
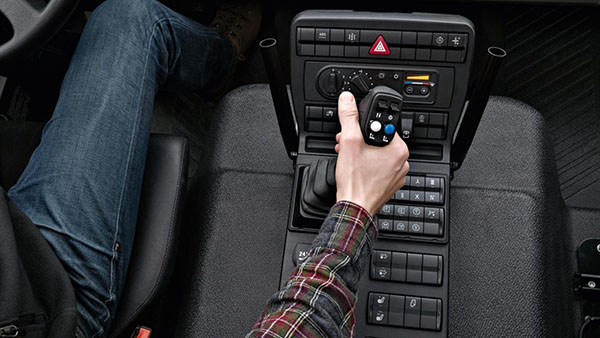
The Unimog is a capable on and off-road vehicle for day-today use and has a configuration to suit the varying needs of business. The practically-oriented workplace and the cockpit has been optimally adapted to suite operators, designed to create the best possible working environment. That helps ensure that every task can be carried out with full concentration and a relaxed approach. For example through the arrangement of controls within easy reach.
A comfortable seating position behind the front axle, air-sprung comfort seats with 3-point seat belts, head restraints and seat heating, as well as auxiliary heating and an air-conditioning system - the panoramic cab of the Unimog implement carrier fulfils high demands in terms of operation, safety and comfort. That helps ensure that every task can be carried out with full concentration and a relaxed approach.
The standard height- and tilt-adjustable steering column allows for an optimal seating position for the driver.
Vision
The front-end dimensions and the position of the driver are especially important when working with front-mounted implements. Unlike the majority of bonneted vehicles, the short nose of the Unimog gives much greater visibility of the working areas to the front, especially when large implements such as snow ploughs are fitted.
In the Unimog, the line of sight reaches the road much closer to the vehicle, reducing blind spots and providing optimal all-round visibility thanks to its large-scale panoramic glazing, the driver's seating position and the short front-end dimensions. The Mercedes-Benz Unimog thus helps actively ensure that the driver recognises dangerous situations early on and can thus also react more quickly to them. And that advantage can be made even better thanks to the optionally available camera system with up to three cameras and a single monitor.

Operating Concept
The operating concept of the implement carrier has been tailored to the needs of operators and drivers: the Unimog's instrument cluster can be controlled using the multi-function steering wheel. There the driver can check the vehicle's oil level, air pressure and alter the Unimog's hydraulic system settings. Gear selection, engine brake activation and the EasyDrive synergetic traction drive system are controlled via the steering column.A removable multifunction joystick can be found in the centre console allowing the operator to control vehicle speed and implements. Operation is especially flexible and the user can control the system in accordance with their needs and desires.
The Unimog features many practical stowage compartments and includes a CD/radio with Bluetooth® hands free mobile phone connection.
Powerful air-conditioning and heating system.
Those spending longer periods of time in the new cab will appreciate the efficient air-conditioning and heating system: regardless of the weather, it ensures comfortable temperatures in the vehicle. Whilst, in winter, the heated seat function can be switched on. To allow work to start punctually there is a programmable auxiliary heating system. Heated windows and mirrors ensure clear vision right from the start.
Multifunction joystick.
A removable multifunction joystick can be found in the centre console allowing the operator to control both vehicle speed and implements. It is also used to operate the synchronised Electronic Quick Reverse (EQR) reversing group.
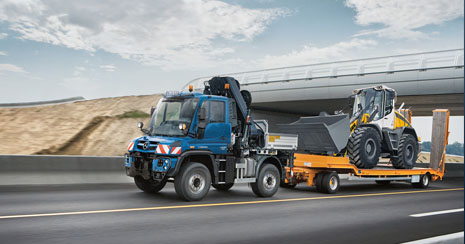
The Unimog implement carrier is equipped with the most modern Mercedes-Benz BlueTec 6 technology. Tested in large-scale series production, the Euro VI engine generation sets new standards for its class and takes no half-measures where conserving the environment, economic efficiency and top performance are concerned. The 4 and 6-cylinder engines ranging from 115 to 220 kW are especially easy to maintain, economical, smooth-running and powerful. They have high torque of up to 1200 Nm as well as good results for exhaust emissions, consumption and power-to-weight ratios. 4-valve technology and common rail injection up to 2400 bar further increase efficiency.
Perfectly tuned drive system technology.
The engines are also used for braking: the strong premium engine brake reduces mechanical wear and tear on the brakes and makes a great contribution to economic efficiency.
The exhaust gas aftertreatment system uses BlueTec 6 technology which has already proven its worth in daily use over many millions of kilometres in our heavy-duty mass-production engines. In the exhaust gas aftertreatment unit, the SCR catalytic converter reduces the nitrogen oxides to a minimum. And the diesel particulate filter prevents almost any soot particles from escaping.
With the U 423, U 429 and U 529 models, the Unimog implement carrier is available with modern Mercedes-Benz engines (OM 934/OM 936, 4 and 6-cylinder) in Euro V and Euromot IV versions. In these versions, no diesel particulate filter, camshaft adjustment and HC metering is used. As a result, such things as the maintenance and life cycle costs are reduced. The general model variant of the three vehicle types corresponds to the basic concept of the current implement carrier model series.
Combined with emissions level Tier4f, approval as an agricultural tractor is possible. Providing the highest economic efficiency in these applications. The Unimog fulfils the emissions standards applicable to tractors.
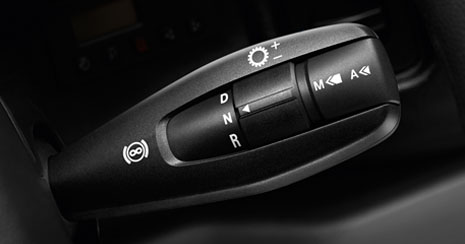
In the Unimog, the fully synchronised electro-pneumatic transmission with its eight forward and six reverse gears provides the tractive power. Unimog is characterised by reliability, robustness and efficiency. And the synchronised Electronic Quick Reverse feature makes it easier to change direction quickly, for instance, during snow-clearing or manoeuvring. There is also the option of a forward-reverse switch which can be integrated into the multifunction joystick.
Total control, total relief: automated shifting.
Two drive programs help reduce the driver's workload: in automatic mode "A" – whilst taking into account the load, accelerator position, engine operation, climbs/inclines and the engine brake – the drive program handles gear changes and clutch operation entirely. However, if it becomes necessary for the driver to manually change gear using the multifunction lever, this is also possible.
Complete control is offered by the "M" drive program (manual). Here, gear selection is also made using the multifunction lever. The driver determines the gear and the clutch operation occurs automatically.

The Unimog implement carrier is a workhorse. And the fully synchronous manual transmission with eight forwards and six (or optionally eight) reverse gears is true proof of that. The fine graduation in the lower gears allows easier individual adjustment of the speed to the current operations. Rapid changing of direction and rocking free are no problem at all thanks to the truck's synchronised reversing gears: it is possible to shift directly between forwards and reverse gears. The low positioning and modular design are conducive to a low vehicle centre of gravity and low transfer of engine vibrations.
There are three variants of transmission-driven power take-off available. For example, the rapid transmission power take-off with 4-hole flange can be used to drive hydraulic pumps. The rotational speed and direction of the power take-off are the same as the engine speed and its direction of rotation. For implement control from outside the cab, a remote control is also available. Programming of the maximum rotational speed prevents overstepping the permissible upper rotational speed limit.
Equally as powerful is the transmission-driven power take-off with 6-hole flange. For applications whereby a very high power take-up is required, such as for fire service pumps, the third variety – also with standardised 6-hole flange – offers an optimal solution. With a nominal engine speed of 2200 rpm, a working speed of up to 3606 rpm can be attained. Here, too, a remote control for use outside the vehicle is also available.
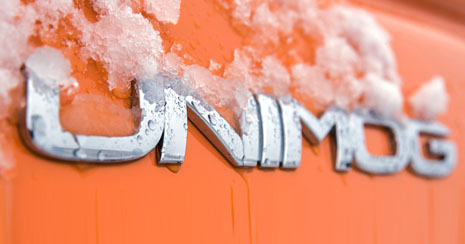
With the Unimog, not only are its users safe on the road, but also other road users. The most important features are: outstanding visibility to the front thanks to the short bonnet; directional stability; ABS; precision steering; optimum axle load distribution; and the workplace with three-point seat belt and head restraint, which is mounted in such a way as to ensure minimal vibrations. The exterior design with its short front-end and very wide field of vision over both the driving and working areas make the Unimog a particularly safe commercial vehicle. The windscreen wiper system is mounted above the windscreen and optimises the cleaning of the windscreen, especially in the case of winter service work. What's more, the headlamps featuring daytime driving lights not only help Unimog users to see better, but also to be seen better. The optional front-end camera and monitoring system also improves vision in the immediate vicinity of the vehicle and makes the mounting of implements easier at the front.
The front-end dimensions and the position of the driver are especially important when working with front-mounted implements. The Unimog minimises blind spots to the front, even when operating with large implements like snow ploughs.
Its balanced axle load ratio is particularly helpful to the Unimog when cornering on slippery road surfaces.
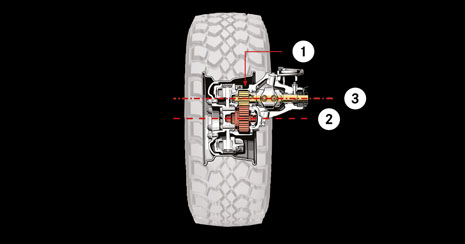
Application versatility is the trademark of the Unimog. Its reinforced portal axles with hub reduction gear guarantee high ground clearance for the most diverse of tasks – even off the beaten track.
To this end, the differential and the drive shafts connected with it are repositioned higher up. The axle tube and differential lie above the wheel centre. In this way, obstacles are easier to overcome and the vehicle's centre of gravity remains low.
Portal axles.
1. Hub reduction gear
2. Wheel centre
3. Axle centre
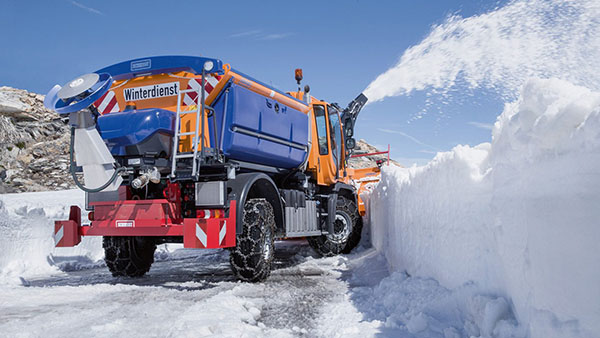
Nothing can unsettle a Unimog.
With its tried-and-tested chassis concept which is based on the robust sub-frame, the Unimog can master even the biggest of challenges in tough everyday operations. Characteristic features are permanent all-wheel drive, great ground clearance resulting from the use of portal axles, high ride comfort, excellent axle articulation and differential locks on both axles. The implement carrier's single tyres, Tirecontrol Plus central tyre inflation system and optimal weight distribution mean it is in its element, even off the beaten track.
Even more agile thanks to all-wheel steering. The optional rear-axle auxiliary steering available on the models from the U 423 to the U 530 serves to reduce the turning circle by a further 20 percent. Accordingly, the vehicle's manoeuvrability also benefits from this in operations during which every centimetre counts. Four types of steering are available: normal steering, all-wheel steering, manual steering and offset track steering (so-called "crab steering"). This variant can help counteract downhill force. When reversing, only the rear wheels steer.
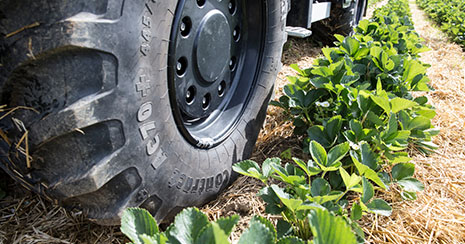
The Unimog is unchallenged: setting the right tyre pressure for the task at hand is conveniently carried out at the push of a button on the display. The driver has the choice between the three pre-configured modes "Road", "Sand", "Rough" and "Manual". The tyre pressure is then automatically adjusted. Thus, the Unimog can be driven with low tyre pressure on loose ground such as sand or mud and hence has a greater tyre contact area. That leads to better traction, less slipping and less damage to the land - including growing crops. Or economical and safe driving on-road thanks to a high tyre pressure and smaller tyre contact area.
The Tirecontrol Plus central tyre inflation system is available ex factory and no special conversions are necessary.
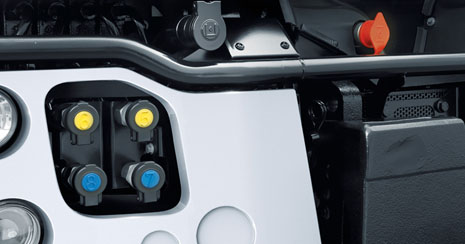
Excellent hydraulic performance which is more precise than ever before: the working hydraulics control implements precisely and without jerky movements. With this in mind, the fully proportional hydraulics system increases efficiency in daily operations. The working hydraulics allow for two positioning movements to be carried out at the same time – simply by using the multifunction joystick. Further functions can be set via the steering wheel buttons. Larger trailer tipping cylinders can also be filled with up to 30 litres of hydraulic oil to draw on as required.
The four-cell working hydraulics and communal hydraulics in accordance with the EN 15431 norm that are used on the implement carrier feature two circuits. Circuit I controls up to eight implement adjustments with a system pressure of 200 bar (32 l/min) over two to four dual-operation valves; alternatively it drives hydraulic motors at the lower output range. When combined, circuits I and II (32 plus 55 l/min) can now mobilise an impressive 35 kW at up to 240 bar. Positioning movements and the powering of hydraulic motors can be carried out independently of one another.
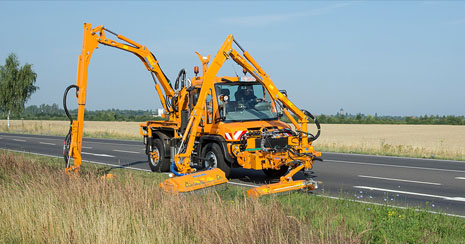
The load-sensing system is a hydraulic control mechanism in which the pressure and/or flow volume of the hydraulic pump is/are adapted to the conditions required by the consumers. In regular hydraulic circuits, the flow volume to the motor is throttled by means of pressure restriction valves or pressure control valves. The hydraulic pump always supplies the full power, even in the case of the flow volume being throttled. In some cases, this can cause high power losses. The load-sensing system, however, ensures that the pump only supplies the flow volume which is currently required for all active consumers.
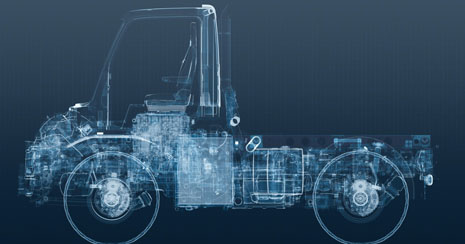
Two circuits, both with 125 l hydraulic oil through-flow per minute and 280 bar pressure: the VarioPower® power hydraulics don't shy away from work, however hard it may be. Regardless of whether several different tasks have to be carried out simultaneously or a single job requires high output. The two open circuits III and IV have the same high through-flow of 125 l/min, system pressure of 280 bar and a maximum output of 58 kW. Operation via the steering wheel buttons of the multifunction steering wheel means it is particularly easy to control. All the settings are displayed in the new instrument cluster.
Tipping hydraulics | 20 l/min, 185 bar |
Working hydraulics (Single circuit) | Working hydraulics |
Working hydraulics (Dual circuit) | 32 l/min, 210 bar (circuit I) |
55 l/min, 210 bar (circuit II) | |
87 l/min, 240 bar (circuit I + II) | |
Load-sensing hydraulics | 110 l/min, 240 bar |
Power hydraulics (Circuit III) | 125 l/min, 280 bar |
Power hydraulics (Circuit IV) | 125 l/min, 280 bar |